This is how it all started…
Many years ago, I had the opportunity to switch from the sector I was working in (infrastructure design) to renewables.
It seemed like an extremely interesting world to me, and I decided to start writing a blog to report on what I was discovering and what I found most interesting.
15+ years later the website is still up and running.
A lot has happened in the meantime – for example, three children have arrived, making it increasingly difficult to find the time to update it.
I hope you will excuse me if I am unable to write often. Of course if you feel like collaborating and sharing content you are welcome!
Happy reading, Francesco
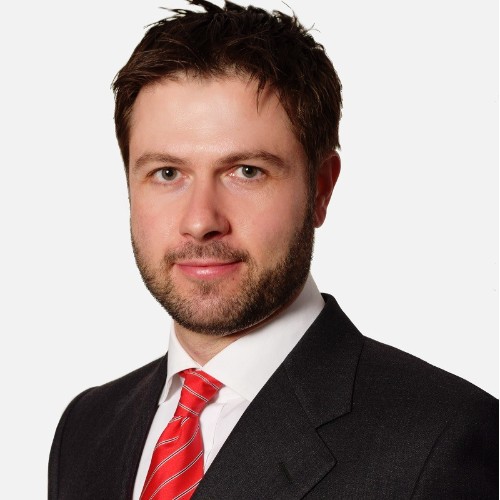
Francesco Miceli
Writer & Engineer