The constant search for higher rated power, taller towers and longer blades has pushed wind turbine manufacturers in an arms race to secure a position in an extremely competitive market.
Today in the onshore market there are machines with rated power close to 6MW, hub heights in a range of 150-165m and blades longer than 80 m. Several projects are currently under development considering these massive sizes.
Lately I have had the opportunity to analyse in depth a new solution which is emerging as an alternative to the traditional lattice boom cranes: the tower cranes.
I have analysed two scenarios, one with the standard lattice boom crane and an alternative scenario with the tower crane.
Standard scenario: lattice booms crane
Lattice boom cranes such as the Liebherr LG1750 have been the standard solution for the installation of the latest generation of turbines, with a tower height in a range up to 140+m.
This type of crane can be moved fully assembled between positions under certain assumptions (such as a very low road longitudinal slope and minimum road width of more than 6m).
If the crane has to be dismantled a substantial area for the boom assembly and disassembly process will be needed (in red in the image below).
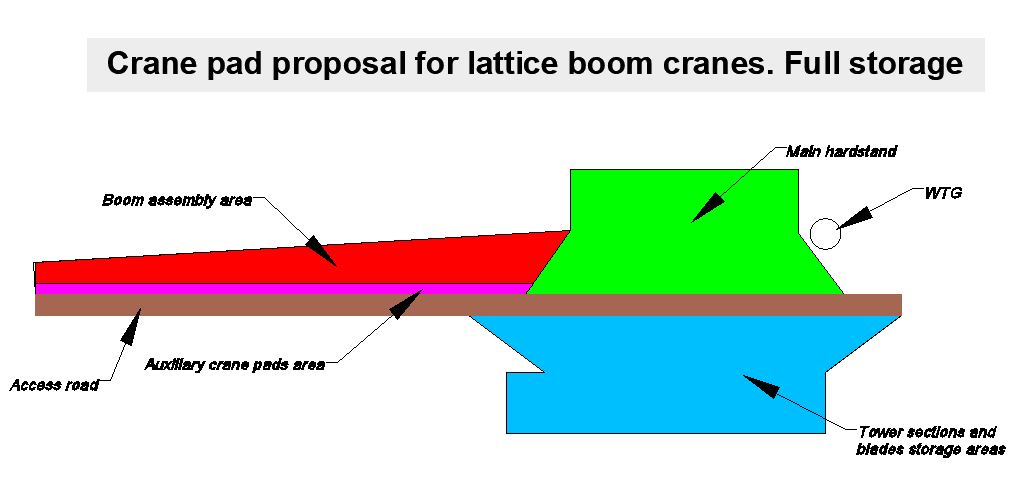
Other characteristics that can have an impact on the project are:
- A mountainous landscape: in this case the boom assembly area would be even more essential. This will have a substantial impact of civil works cost.
- Very high installation rates (such as 3 or 4 turbines per week). The limited stock of lattice boom cranes suitable for this hub heights worldwide create a risk: either you book the cranes two years in advance (giving up the possibility of changing the schedule) or you wait – with the risk of losing the crane availability slot.
Alternative scenario: tower cranes
The idea of using tower cranes for wind turbines installation is not new in the onshore sector.
Said that, as far as I was aware of, the use of this typology of cranes has been negligible in the last few years.
Not so many references can be found in America or Europe. One example would be the installation of Gamesa’s G114 of 2,5MW 156m steel tower at the Borja Wind farm (Spain). The crane used was the Liebherr 1000 EC-B 125.
Common sense tells me that the experience turned out not to be very positive (otherwise I presume that the concept would have been replicated, while that does not seem to be the case).
More recently, new models from Krøll Cranes have been used in wind farms at the opposite side of the planet, in Thailand and Australia.
Big players like ALE are suggesting that this new concept is reliable.
One of the main references is the Theparak wind farm project in Thailand, where 60 V136-3.0 MW where installed using this crane.
Here we have a list of some of the projects installed in Thailand with tower cranes:
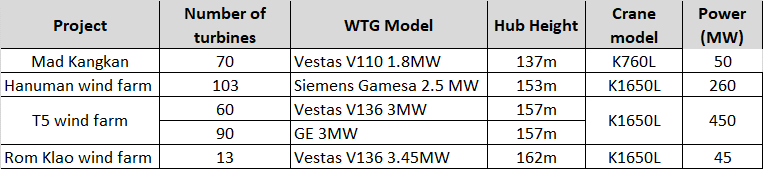
The main pros of the tower crane are:
- Road width required: only 4.5 m (even as little as 3.5 m according some sources).
- Cranes boom is only 70 m long.
- Advanced crane bases allow savings in the critical path.
- Lower minimum lifting radius compared to lattice boom areas.
- Installation rates about 2 hours per component. An installation rate of 1 WTG every 4 days has been reached in the Thai projects.
- Operational up to wind speeds of 15m/s.
On the other hand, cons would be:
- Lack of experience of the operators with these new set of cranes and low offer worldwide.
- Uncertainty on the actual installation rates due to insufficient track record.
- Real installation costs are still unknown.
Depending on the characteristics of the project, Kroll cranes has available these models:
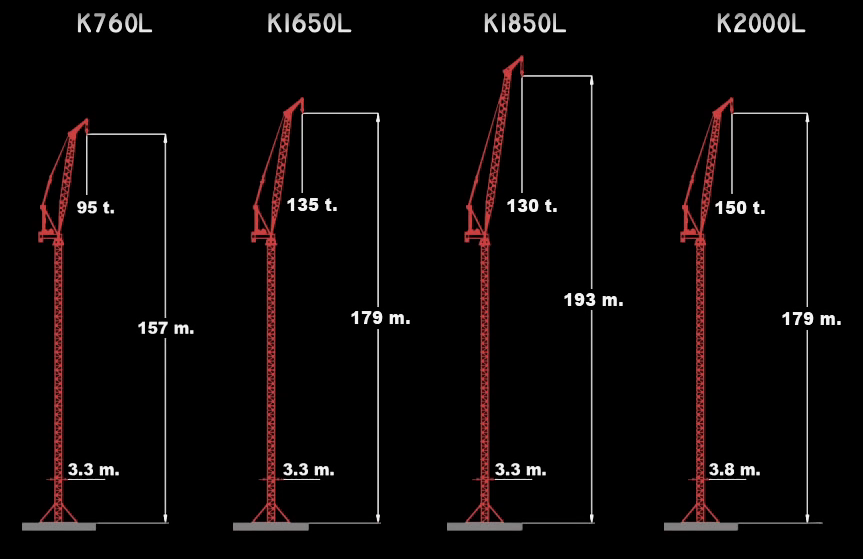
How would an hardstand layout adapted to both the tower crane and the new generation of turbines look like?
It seems that a tower crane could work using a standard hardstand without the boom area:
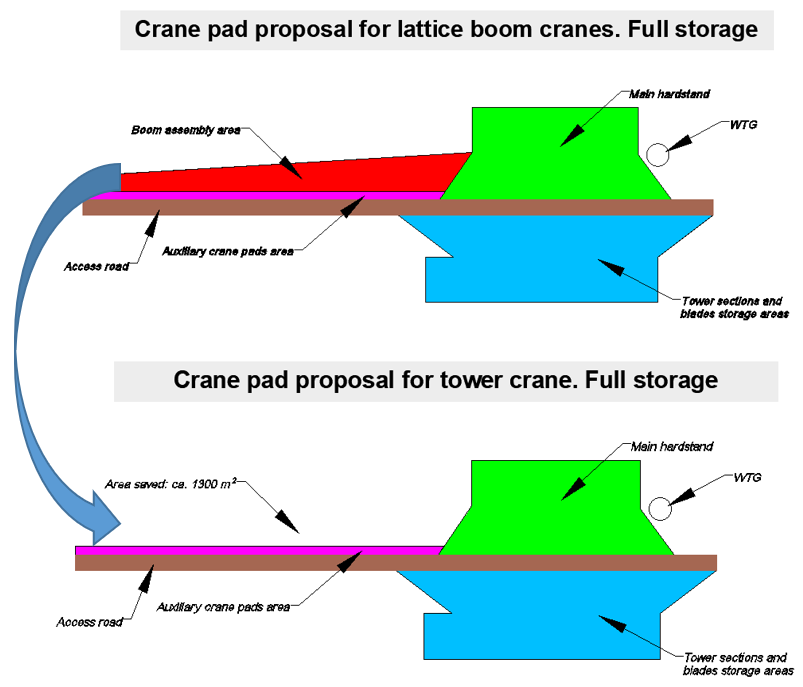
Some 3d models where created on real WTG locations to assess the actual impact on cost of this new configuration. Quantity reductions in topsoil stripping, excavation and fill material may lead to a cost reduction around 5000€ per hardstands (being conservative).
A nice image with a 3D model of the hardstand analysed is included below:
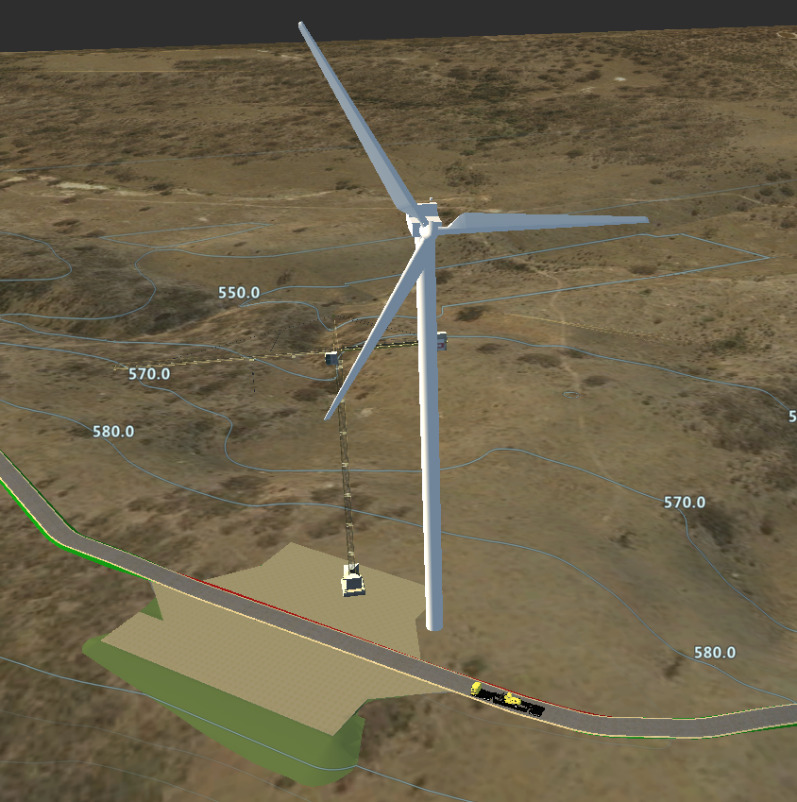
Even if potential savings in the civil works seem to be easy to achieve, a real total project cost reduction can be confirmed only considering the actual installation costs, which are not so clear at this moment.
Are tower cranes going to be a more mainstream solution in the future?
Only time will tell.
Addenda (21/04/2021)
I have received this email from Jasper from Lighthouse projects. I think it
can be useful to other readers.
Regarding the tower cranes in compare to Crawler crane I would like to share with you some experience.
I have worked 2 years ago at windpark Krammer which consists out of 34 Enercon E115 turbines on a dyk with no space for storage components or installation of the cranes.Therefore we have used 2 Liebherr EC1000 Tower cranes in the project to build the wind turbines.
My experience is that with the limited space on site it is easier to install the crane. Another benefit is that crane capacity because the crane can lift up to 100t we could pre assemble the rotor and generator up front and lift the generator in one lift which is efficient. In addition what we saw is that you can lift longer you can lift up to 12 m/s or more.
A disadvantage of this type of crane is that it must be extended at some point. Mast sections must then be placed in between so that the hook of the crane becomes higher.
Leave a Reply